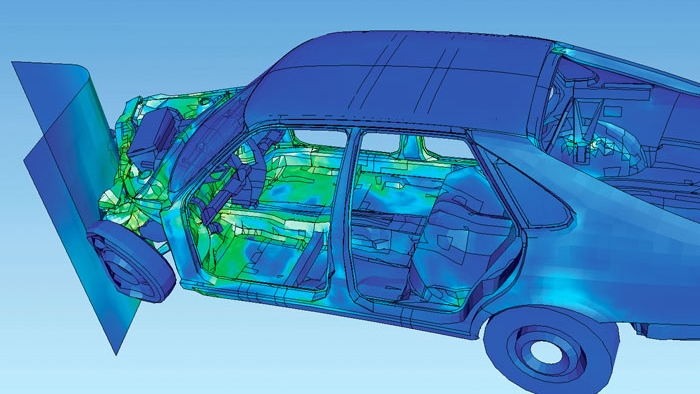
Guest writer Michael Hiller MSME is a principal at In2solutions.com with over 20 years of experience in CAD, FEA, and other numerical methods for product development in dozens of industries. Industry-leading companies recognize the benefits of CAE and invest millions to develop and maintain in-house assets. If CAD is the first cornerstone of CAE product design capability, then finite element analysis (FEA) is certainly the second.
What exactly is FEA and how does it work?
CAD (Computer Aided Design) facilitates the definition, refinement, and communication of product shape and fit, whereas FEA predicts its physical behavior and performance. Products of all size and sophistication can be developed faster, better, and at lower cost and risk by leveraging advanced computer aided engineering (CAE) software technology.
FEA is a numerical method that discretizes CAD geometry into small blocks called nodes and elements so that physics and engineering calculations can be solved to predict how the system will perform in the physical world.
These are the same calculations you'd perform manually on a solid, beam, or pipe, but the FEA software automatically does thousands or millions of calculations for you.
Test how your 3D model will behave in the real world before you invest in any tooling: Improvement is assured in virtually all cases
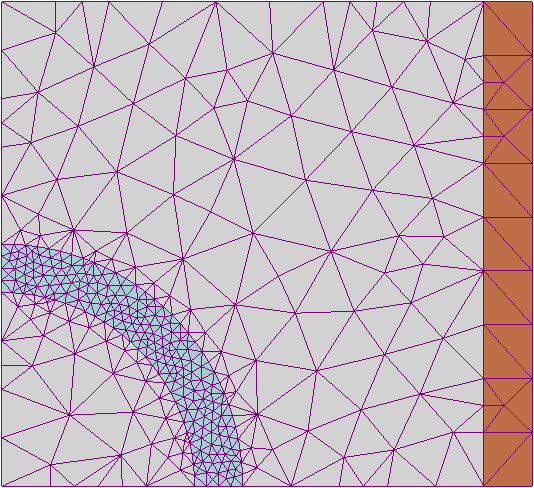
The discretization process is called “Meshing” and is typically performed on 3D, fully detailed geometry nowadays, but simplified geometry and even 2D idealizations can often be leveraged to provide faster answers by reducing the amount of nodes which speeds the calculations. For optimal efficiency we strive to use enough nodes to achieve accuracy, but not so many nodes that calculations become onerous.
If you have an inkling of your geometry and load scenarios then even preliminary FEA can be setup and run! Estimates and approximations can be made for any unsettled aspects of your design, and FEA can be performed to identify any problems and improve the design, especially since we can perform “comparative FEA” to focus on “percentage improvement” instead of absolute results. Improvement is assured in virtually all cases. FEA can be linear (behavior that is reversible and proportional), or it can be non-linear and even path dependent, such as when friction and/or hysteresis is incorporated.
Simple and Quick linear FEA can be performed in hours or days, while large and/or complex models such as large aerospace or nuclear projects may take weeks or months. ROI's can be very compelling -- in all types of situations, the value of the information far exceeds the cost.
It's important to discuss and define the goals of an FEA project upfront. Simple/quick FEA is often performed on design concepts, while more detailed and exact simulations are incorporated as the design solidifies. The knowledge obtain from FEA at all stages leads to improved designs, lower costs, and lower risk.
The FEA process "tests" your design in the digital world and is akin to virtual reality recreations
FEA almost always plots more result variables, and provides a more complete picture of product performance, compared to physical tests which have time, cost, and sensor-channel limitations.
While there is great benefit to validate your FEA results with actual tests, you will find that the FEA actually provides a more complete picture of product performance at every surface, feature, and nook and cranny whereas it's impossible to instrument the entire geometry in the real world.
Numerical predictions and optimizations can be performed at every stage of the product development and DFM cycle. With FEA we can "test" and improve the early design in minutes for dollars, whereas it might cost thousands and take weeks or months to identify and incorporate design improvements later.
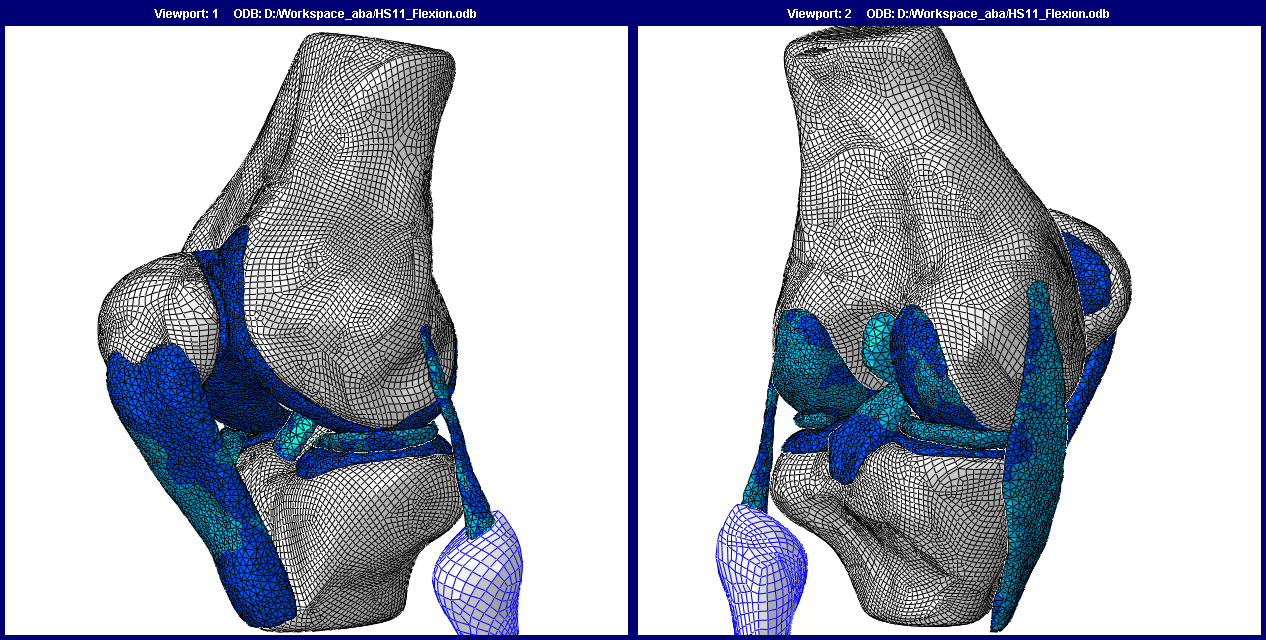
The latest FEA software integrates well with everyone's CAD and product development process. Geometry updates from the CAD system and/or geom tweaks within the FEA environment can often be incorporated easily without having to start from scratch anymore. Time and money are saved, and more design-iterations and “what-ifs” can be tried!
The benefits of FEA testing
FEA can predict performance such as: Structural, Thermal, Magnetic, Fluid/CFD, wireless (iot), as well as drop & crash impact. Nearly every product design or concept benefits from FEA:
- Leverage FEA on design concepts as well as nearly finished designs, or even forensic work when existing designs fail
- Predict product performance and compliance earlier in the design cycle
- Leverage FEA for what-if scenarios, comparative studies (to existing and/or competitive products), and well as failure/forensic investigations
- Test more variables, materials, loads, and actually render results in greater detail than physical testing allows
- Make greater strides in innovation, yet reduce risks and costs
- Plots, Animations & Reports deliver technical advantages, plus become business/marketing assets as well
- Optimize products before prototyping to reduce time to market, cost and risk
Trig recognizes the benefits of ANSYS FEA and has teamed with NC-based In2Solutions.com to provide Product Analysis & Optimization services that will support and accelerate Innovation at Trig.
---------
In2Solutions brings over 20 years of industrial as well as "insider" FEA expertise. In2Solution's president, Michael Hiller (BSME, MSME), worked in two different ANSYS ASD sales-channel territories assisting hundreds of customers in all types of industries-- that varied and proven “insider” expertise delivers special efficiency and greater success on every project.
More info is at www.in2solutions.com. Touch base with a Trig team member to discuss leveraging the benefits of FEA for your next project.