The product development process is a multi-stage endeavor
Informed by customer research and marketing analysis, strong opportunities drive the first legs of the race to get a product onto shelves. When the project is handed off to development, it is in these stages that opportunities become designs, and designs become products. For creating products with any measure of human interaction, incorporating industrial design can make or break the success of the end result. In the last three stages of the development relay, design will distill innovation into a concept, engineering will take the baton and optimize the concept for production, and manufacturing will cross the finish line after turning the fine-tuned blueprint into a product.
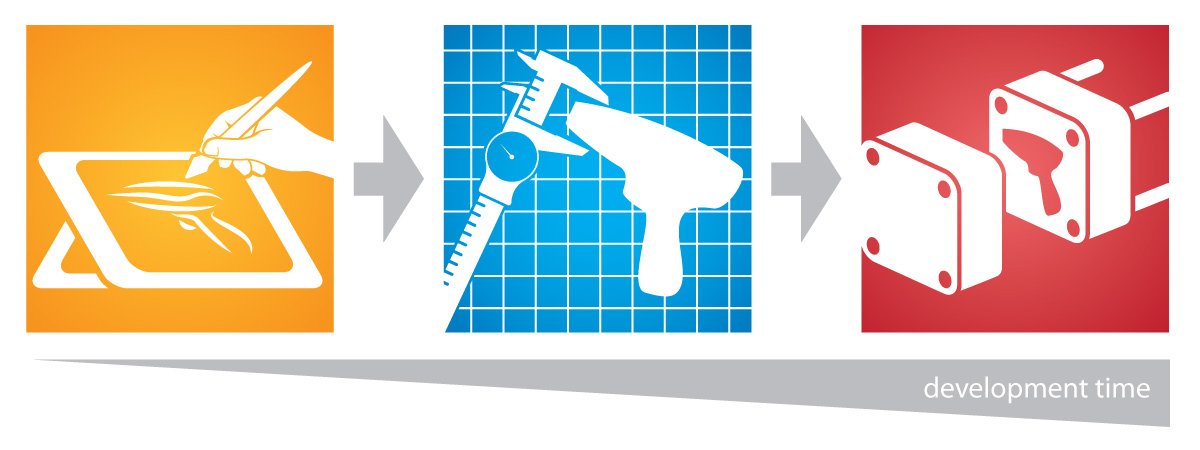
In the design, engineering, and production legs of the race, the relay requires a high level of collaboration and trust among the groups responsible - no leg is more or less crucial to the vitality of the finished product than the others. The end goal is always dual in nature: create a product that embodies the functional concept and satisfies the end user; create a product in a timeframe short enough to be efficient. If the actual race is run correctly, with great transitions, the team is likely to fulfill the first objective. The second goal is attained much less often, or, at least the team usually sees ways that they could have finished more quickly.
This three-step relay has the benefit of stable process for tackling large, complex development initiatives, but this stability comes at the price of efficiency and loss of design intent—especially when developing solutions of low-to-moderate complexity.
Is this sacrifice necessary? Now, the links among the roles in product development have been blurred, as firms structure their processes in ways that make waiting for the torch to be passed—and even passing it in a certain order—notions of the past. Indeed, innovative industrial design and precise engineering can occur concurrently, placing uncompromised design intent and engineering specifications in the service of manufacturers.
At Trig, we relish the challenge of achieving design that transcends these sometimes competing constraints. Holding each of the three concerns in balance through the product development process has proven to be a source of great innovation many times over. Our industrial design team has mastered the craft of executing on both fronts—design and engineering—during our development process. Good design considers the end user, nurtures and evolves brand language, increases utility, decreases complexity, and differentiates a product for market success. Some projects, however, require an additional degree of rigor on our part: that we keep manufacturing parameters at the forefront of the process, not to inform the design, but to optimize it for production in the most efficient way possible.
It is difficult to imagine pursuing many product development initiatives without the efficiency and precision of injection molding, or the speed and robustness of CNC machining. A multitude of manufacturing processes lie at the disposal of product developers today, but each requires more than a topical knowledge to execute successful designs and preserve intent. Trig Innovation has strong capabilities in designing for injection molding, zinc casting, extrusion, sheet metal fabrication, CNC machining, and many others.
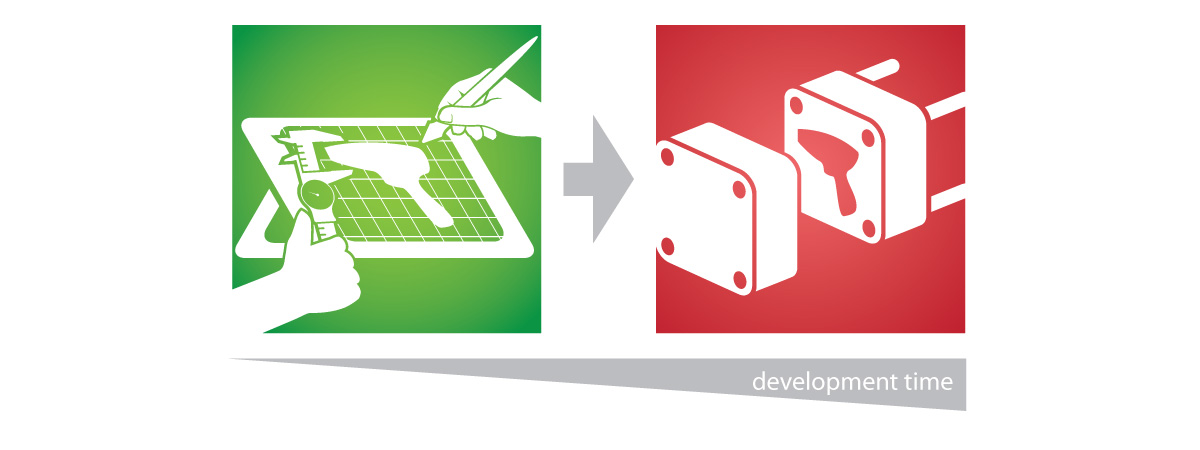
Our product design skill set blurs the traditional line between industrial design and manufacturing engineering, as years of experience and dozens of projects have forged our knowledge of various manufacturing practices. We can execute simple or complex injection-molded parts with zero loss of design intent, create dynamic mechanical assemblies to analyze a product’s operation, and optimize designs for 3D printing to test functionality in-hand before a single dime is invested in tooling. These capabilities enable us to execute quick-turn design projects ready to hand off to production, and our adaptability makes it easy to integrate our services into any workflow for responsibilities both large and small.
Are you ready to leave compromise of your concepts behind, and still achieve speedy market entry? Trig can help.
For related case studies in the industrial design and product development of consumer products, check out our work with startup, SEAL SwimSafe